Centres d’usinage
- 1. Principales fonctions et caractéristiques
- 2. Émergence et développement des centres d’usinage
- 3. Structure générale et types de centres d’usinage
- 4. Différences entre les centres d’usinage horizontaux et verticaux
1. Principales fonctions et caractéristiques
Aujourd’hui, les centres d’usinage sont très répandus sur les sites de production. Outre leur finalité première, la fabrication de matrices, ils sont également employés pour usiner des pièces et composants métalliques. Par exemple, dans l’industrie automobile, les centres d’usinage sont exploités pour façonner des matrices pour pièces de carrosserie mais également pour meuler et percer plus efficacement les composants de moteurs. De nombreux autres produits couramment utilisés dans notre quotidien et en milieu industriel sont fabriqués par des centres d’usinage.
Les centres d'usinage sont dotés d’une fonction de changement d’outil automatique par calculateur. Sur une machine-outil à commande numérique classique, l’opérateur doit procéder manuellement aux changements d’outil. Les centres d’usinage sont équipés d’un bras automatique qui retire l’outil utilisé et procède à un échange à partir d’un magasin d’outils. En cours d’usinage les changements d’outil sont plus rapides et plus faciles, garantissant un fonctionnement automatisé et économe en énergie tout en réduisant les coûts.
Depuis quelques années, l’émergence des centres d’usinage à cinq axes, intégrant deux axes rotatifs en plus des trois axes habituels, permet l’usinage de formes toujours plus complexes.
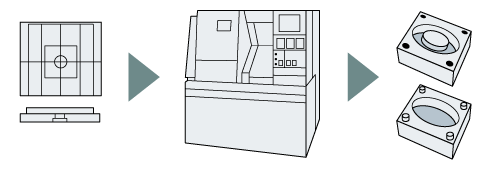
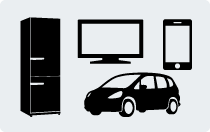
2. Émergence et développement des centres d’usinage
La fabrication de pièces métalliques implique généralement le meulage de surfaces et rainures après application de procédés d’usinage complexes tels que le perçage, l’alésage (élargissement de trous) et le filetage. Auparavant, différents outils de coupe, tels que des fraises à surfacer, des fraises en bout, des forets, des outils d’alésage et des tarauds étaient individuellement utilisés en fonction du procédé.
Plus tard, avec l’émergence des tours à commande numérique, un mécanisme de changement d’outil manuel appelé tourelle a été développé, facilitant les changements de lame. Les centres d’usinage vont encore plus loin, en proposant un changement d’outil automatisé, commandé par calculateur. Les centres d’usinage sont capables d’exécuter simultanément plusieurs procédés d’usinage sur différentes surfaces d’une pièce, améliorant ainsi considérablement la productivité. En perpétuelle évolution, ils gagnent en précision et en vitesse d’année en année, devenant l’équipement incontournable de tout site de fabrication.
Visitez n’importe quelle usine de métallurgie, vous y trouverez nombre de centres d’usinage travaillant sans relâche jour et nuit. Seuls quelques opérateurs sur site sont requis pour surveiller le fonctionnement des machines.
Sur les tours à commande numérique, les outils sont montés sur une tourelle, pivotée manuellement.
- A
- Tourelle
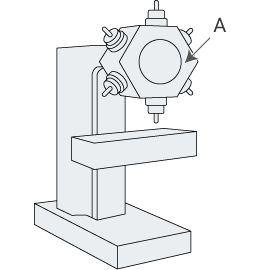
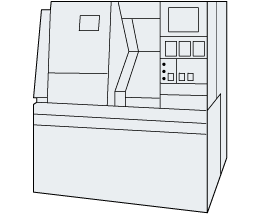
3. Structure générale et types de centres d’usinage
Les centres d’usinage se déclinent en trois principales catégories en fonction de leur structure : horizontal, vertical ou à portique. Sur les centres horizontaux, premiers développés, la broche surmontée de l’outil de coupe est fixée à l’horizontale (soit parallèle au sol). À l’inverse, sur les centres verticaux, la broche est fixée à la verticale. Sur les centres à portique, la broche est fixée au plafond du portique, tête vers le bas.
Prenons pour exemple une configuration horizontale, la structure générale d’un centre d’usinage est composée d’une partie support appelée banc, d’un chariot qui se déplace sur le banc, d’une table fixée sur le chariot destinée à accueillir le matériau brut, d’une colonne installée perpendiculairement au banc et d’une broche sur laquelle est monté l’outil.
4. Différences entre les centres d’usinage horizontaux et verticaux
Les centres d’usinage horizontaux sont équipés d’une broche porte-outil latérale, qui usine les pièces suivant une direction horizontale. La colonne se déplace le long de l’axe X, le chariot le long de l’axe Y et la table le long de l’axe Z et cette combinaison permet un usinage en trois dimensions. De plus, certains modèles présentent un axe B permettant une rotation de la table à l’horizontale, pour un usinage suivant quatre axes.
L’un des avantages du centre d'usinage horizontal est sa capacité à usiner simultanément quatre surfaces d’une même pièce, dans le cas d’un centre à quatre axes. L’opérateur n’a plus à tourner manuellement la pièce pour changer de côté, contribuant ainsi également à améliorer la précision. De plus, l’usinage à l’horizontale permet une chute des copeaux directement sur le sol, évitant tout risque d’accumulation des copeaux sur la pièce et autour de l’outil.
À l’inverse, les centres d’usinage verticaux présentent une broche fixée à la verticale, qui usine les pièces par le dessus. En règle générale, la table se déplace horizontalement suivant les axes X et Y et la broche se déplace verticalement, permettant un usinage suivant trois axes.
Comparés aux centres horizontaux, qui imposent une installation latérale, les centres verticaux sont moins encombrants, ce qui fait leur succès. De plus, l’usinage par le dessus permet aux opérateurs de travailler en comparant la pièce au dessin de conception. Cependant, cette technique implique également un risque d’accumulation des copeaux sur la pièce et exige l’utilisation d’un souffleur à air comprimé ou l’exécution d’un rinçage au lubrifiant pour se débarrasser efficacement des copeaux.
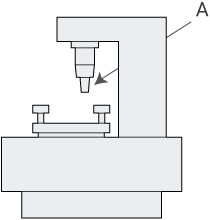
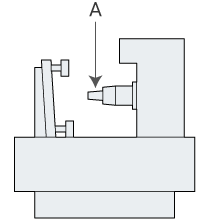
- A
- Broche surmontée d’un outil