Tours à commande numérique
- 1. Principales fonctions et caractéristiques
- 2. Principaux types de tours à commande numérique
- 3. Évolution des tours à commande numérique
1. Principales fonctions et caractéristiques
Depuis leur invention, dans les années 1950, les machines-outils à commande numérique (NC) ont considérablement fait avancer la métallurgie. Des opérations, auparavant exécutées manuellement, pouvaient enfin être automatisées. Peu après leur sortie, les machines-outils à commande numérique ont intégré des calculateurs, la machine-outil à commande numérique par calculateur (CNC) était née.
Notez que les premiers tours à commande numérique ont été développés dans une université japonaise à la fin des années 1950. Par la suite, les tours existants ont été équipés en standard de servomécanismes. Ces deux avancées majeures ont contribué au développement du tour que nous connaissons aujourd’hui.
Un tour est une machine-outil qui met en rotation un matériau cylindrique et découpe les parties inutiles en plaçant un outil de tour (outil de coupe) contre ce matériau. Outre le tournage au moyen d’un outil droit à charioter classique, le tour permet d’autres procédés, tels que le perçage, l’alésage, le rainurage et le filetage.
Un tour à commande numérique peut employer plusieurs dizaines d’outils différents au cours d’une procédure d’usinage programmée et automatisée par commande numérique. Grâce à la commande numérique, il est possible non seulement de commander avec précision la position de découpage ou autre usinage via l’utilisation d’un système à trois axes mais également de gagner en flexibilité, en commandant la vitesse de rotation et la vitesse d’avance de l’outil en fonction du matériau de la pièce et de la forme souhaitée.
2. Principaux types de tours à commande numérique
L’usinage au tour permet de créer différentes formes selon l’outil de coupe utilisé : outil droit à charioter classique, outil à saigner, outil à aléser, etc. La capacité à utiliser un jeu d’outils en continu sans changement permet d’améliorer l’efficacité de l’usinage et prévient la dégradation de la précision, inévitable en cas de changement d’orientation de la pièce ou de changement d’outil.
Les tours à commande numérique courants sont généralement équipés d’une tourelle, unité rotative surmontée de plusieurs outils de tour, qui pivote pour passer d’un outil à un autre. Cet équipement permet une transition fluide d'un procédé au suivant en maintenant la pièce en position.
Un tour automatique multibroche est doté de plusieurs broches, lui permettant d’exécuter différents procédés simultanément, pour une productivité améliorée. À l’inverse, un tour automatique monobroche permet l’exécution d’un unique procédé en continu. Ce type de tour intègre un autochargeur qui charge les pièces automatiquement pour fabriquer des produits de même forme en grands volumes. Parmi les autres machines-outils spécifiques, citons les tours en l’air et tours verticaux, dédiés aux pièces de grande taille, et les tours en fosse pour l’usinage de roues de wagons.
3. Évolution des tours à commande numérique
Aujourd’hui, les tours à commande numérique sont tellement informatisés que la différence avec les tours à commande numérique par calculateur est infime. Dans l’optique d’une productivité toujours accrue, les modèles équipés de plusieurs broches et tourelles, capables d’usiner plusieurs dimensions à la fois en maintenant la pièce en rotation, se généralisent.
Dans le même temps, la précision s’améliore grâce aux tours haute précision qui exécutent des usinages de l’ordre du micron, principalement dans l’industrie des composants électroniques. L’automatisation des fonctions périphériques, telles que l’avance, l’alimentation, le nettoyage et la mesure des pièces contribue considérablement à rationaliser la fabrication.
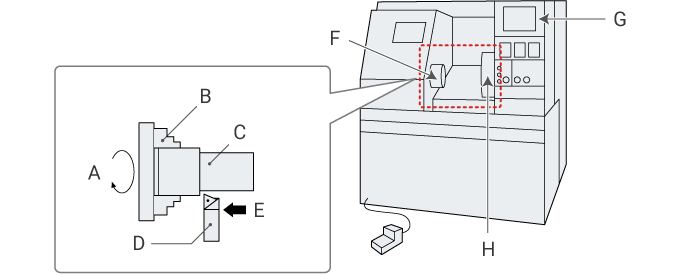
- A
- Rotation de la broche
- B
- Mandrin
- C
- Pièce
- D
- Outil de tour
- E
- Tournage
- F
- Broche
Un mandrin retient la pièce. - G
- Panneau de commande
- H
- Tourelle
Surmontée de plusieurs outils.